Understanding Stainless Steel Grades
Stainless steel is a versatile material used in various industries due to its durability and resistance to corrosion. However, not all stainless steel grades are suitable for every application, especially when it comes to flange connections. Understanding the differences between grades such as 304, 304L, 316, and 316L is crucial for making informed decisions.
Differences Between 304, 304L, 316, and 316L
SS304 is known for its excellent corrosion resistance and formability. It contains approximately 18% chromium and 8% nickel. SS304L is a low-carbon version of SS304, which enhances its weld ability while maintaining similar corrosion resistance.
On the other hand, SS316 includes molybdenum, which increases its resistance to pitting and crevice corrosion. SS316L is the low-carbon variant of SS316, offering better weld ability without compromising on corrosion resistance.
Challenges with Using SS304 for Flange Connections
Mechanical Strength Concerns
SS304 lacks the mechanical strength. This can lead to deformation or failure under extreme pressure or load conditions.
Thermal Expansion Issues
When exposed to varying temperatures, SS304 can expand or contract more than other materials like carbon steel or higher-grade stainless steel. This expansion can compromise the integrity of flange connections by causing misalignment or loosening over time.
Corrosion Vulnerabilities
SS304 can still be affected by specific types of corrosion like pitting and crevice corrosion in environments with high chloride levels.
Disadvantages of Stainless Steel Bolts
Cost Implications
Stainless steel bolts are often pricier compared to options such as carbon steel or alloy steel bolts.
Low Mechanical Strength
They might not hold up well in heavy-duty situations where a lot of pressure is involved. They could stretch or snap when pushed hard.
Welding Difficulties
Welding stainless steel bolts can be tricky because they are prone, to bending and breaking increasing the intricacy and expenses in projects that include welded flange connections.
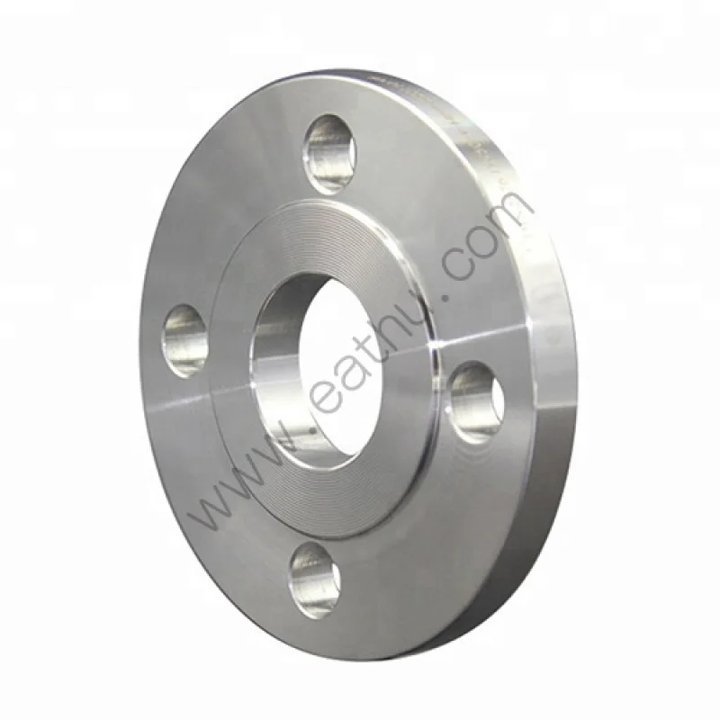
Alternative Solutions for Flange Connections
When tackling the issues linked to SS304 in flange connections some solutions can enhance performance and reliability. Here are a few possible choices.
Use of Carbon Steel Bolts
Carbon steel bolts offer tensile strength that can endure significant mechanical stresses.They are also less susceptible to stress corrosion cracking.
Protective Coatings and Treatments
Protective coatings or treatments can be applied to bolts to boost their durability, against elements that trigger corrosion issues effectively. Coatings like zinc plating or galvanization act as a shield against moisture and chemicals. Additionally, treatments such as anodizing or phosphating can enhance surface hardness and resistance to wear.
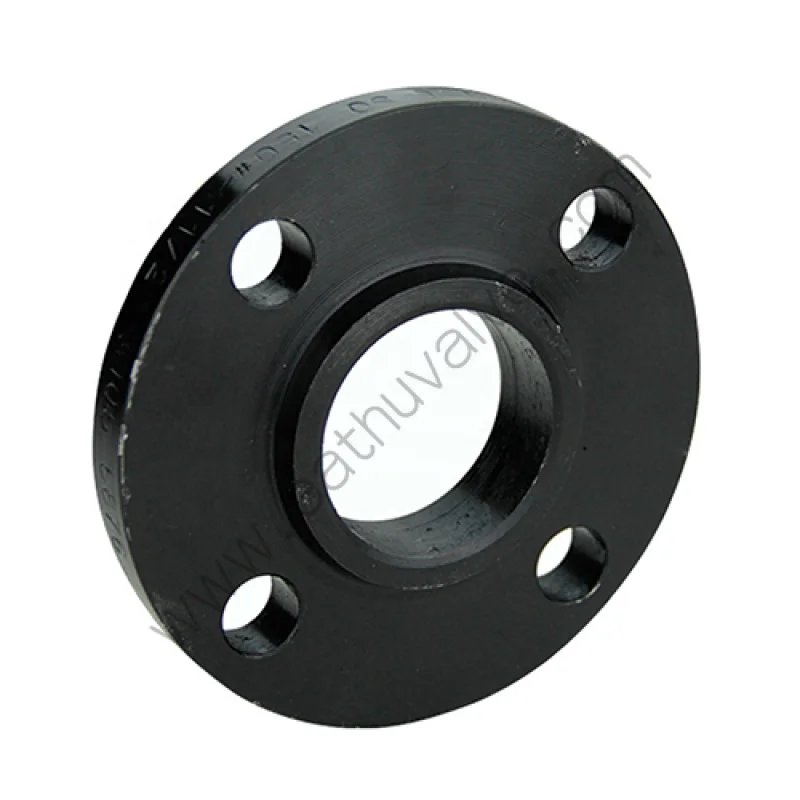
Conclusion: Selecting the Right Bolt Material for Reliable Sealing
Although SS304 has its benefits in some aspects; its drawbacks concerning strength shortcomings and susceptibility to expansion and corrosion issues render it less suitable for certain uses.
To ensure the safety and efficiency of their systems in different applications, professionals need to grasp the requirements and adhere to established standards diligently.For information on cutting-edge solutions customized for demands check out FLUIDO which provides a wide array of products crafted to fulfill varied operational needs.
If you're curious about checking out kinds of flanges that could work well with these solutions in scenarios take a look at Lapped Joint Flange choices as they are versatile and can be used in diverse settings.