Proper installation plays a crucial role in maintaining system efficiency, safety, and long-term performance. This blog explores why valve direction matters and offers specific installation guidelines for different types of valves.
Why Valve Direction Matters in Industrial Systems
The Hidden Impact of Flow Direction on Valve Performance
Incorrect valve installation can lead to serious issues. The flow direction directly influences how a valve regulates pressure, manages leakage, and ensures safety. For instance, improper installation can result in valves failing to close fully, leading to leaks. Additionally, incorrectly oriented valves can cause excessive wear and tear, reducing their lifespan.
Valve-Specific Installation Guidelines
Butterfly Valve Installation Direction
Butterfly valve installation direction is key for regulating flow in large pipelines. Pay attention to the flow arrow and pressure marks on the valve body. These signs help avoid flow blockages.
Horizontal mounting is common for butterfly valves. However, vertical placement works too, depending on the task.
Ball Valve Flow Direction
Ball valves are widely used in industrial setups. Their ball valve installation flow direction is crucial. Many ball valves have a one-way flow design. They handle flow in only one direction.
Installing them backward can lead to poor sealing. This causes leaks or loss of control. Bidirectional ball valves manage flow both ways. Yet, they still need proper placement for dependable function.
Check Valve Installation Direction
Check valve installation direction is critical for preventing backflow in pipelines. Reversed placement can allow backflow. This may harm equipment. It can also disrupt system function.
There are two main check valve types: swing and lift. Swing check valves use gravity to close. They must be installed vertically. Lift check valves work horizontally or vertically. Still, they need precise alignment to operate well.
Gate Valve and Globe Valve Orientation
Globe valves can be installed either way, depending on the task. Consider the stem position during placement. For manual use, place the stem at the top or bottom. This ensures smooth handling.
Gate valves often work best with upward flow. This supports steady throttling. Globe valves may use low-in or high-out flow setups. These provide better control over pressure adjustments.
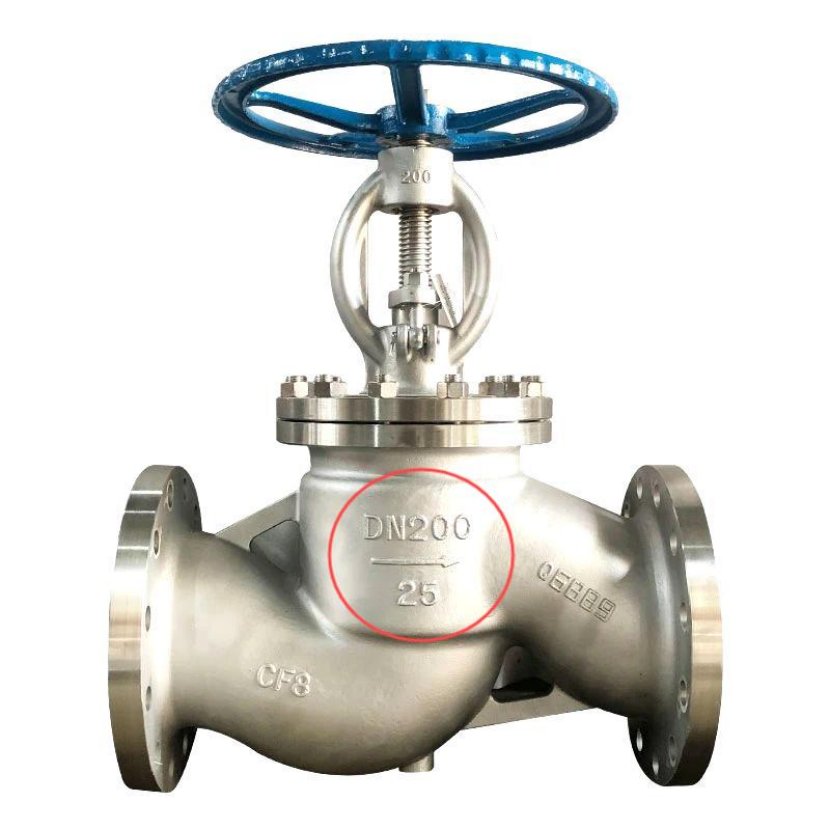
Avoiding Common Installation Mistakes
Specialty Valves Require Special Attention
Specialty valves, like cryogenic or angle valves for sticky liquids, have unique placement needs. Cryogenic valves need proper venting. This handles the very low temperatures in certain industrial tasks.
High-Pressure Systems and Reverse Installations
Sometimes, standard placement rules need tweaks. For example, reverse-seated globe valves suit high-pressure setups. Their flow path may need flipping.
Hazardous Material Handling
Handling risky substances requires special valve strategies. Double-block-and-bleed (DBB) systems isolate hazardous liquids in pipelines. They prevent leaks and spills.
For acidic or corrosive liquids, correct valve orientation is vital. It reduces damage to the valve body and seals. Additionally, rust-resistant materials extend valve life. These withstand harsh substances effectively.
FAQs
· Can I install a butterfly valve vertically if space is limited?
Butterfly valve installation direction allows vertical placement in tight spaces. However, follow maker guidelines for best results.
· What’s the safest way to handle bidirectional ball valves?
Install bidirectional ball valves based on system flow needs. Test them regularly to ensure proper function.
Conclusion: Choosing the Right Partner for Your Automotive Molding Needs
If you aim to enhance your industrial setup with precise engineering, team up with FLUIDO. Our skilled crew ensures every valve is placed correctly. This delivers lasting performance and dependability. Contact us todayfor a free directional review. Discover how we can improve your liquid control setups!